What is Plastic Concrete Formwork and Its Role in Modern Construction?
Plastic concrete formwork, also known as “polymer formwork,” “plastic formwork,” or “concrete plastic formwork,” is an innovative, lightweight mold crafted from high-performance polymers like ABS (Acrylonitrile Butadiene Styrene), PP (Polypropylene), or PE (Polyethylene). It is used to shape fresh concrete in construction projects until it sets into structures such as walls, columns, slabs, foundations, or specialty forms like pools or stairs.
Manufactured in Iran by Alborz Formwork, our plastic formwork systems feature modular designs with pin or lever connections. These systems offer a cost-effective and durable alternative to metal or timber formwork, revolutionizing efficiency and sustainability in the construction industry.
Plastic concrete formwork plays a pivotal role in modern construction by enhancing speed, reducing costs, and improving quality. In a residential tower project in Tehran, our ABS forms, proudly made in Iran, delivered smooth, exposed concrete walls without the need for oiling, reducing labor time by 25%. In a humid villa project in Mazandaran, its rust-free nature outperformed metal forms, saving maintenance costs in salty, wet conditions. With global metal prices rising (e.g., a 20% increase in 2024), plastic formwork’s affordability and practicality, manufactured in Iran, make it a rising star.
Want to know the plastic formwork price or make a purchase from Iran? Contact us at +98 912 139 0683 or visit our Metal Formwork page for comparisons!
Applications of Polymer Formwork in Construction Projects
Polymer formwork’s lightweight design and adaptability, manufactured in Iran by Alborz Formwork, make it a standout choice for construction. Our systems cater to:
Wall Formwork: Shapes concrete walls from boundary to shear walls, with flat panels and corners (internal/external) for precision. A Tehran project used our forms, made in Iran, for 20 cm shear walls with flawless alignment, saving 20% on finishing.
Slab Formwork: Replaces plywood in dala or joist slabs, moisture-resistant and lightweight. A Shiraz factory pour over 400 m² showcased its resilience, all produced in our Iranian facilities.
Column Formwork: Prismatic design adjustable from 20×20 to 60×60 cm, versatile for square, rectangular, or L-shaped columns. An Isfahan villa used our Iranian-made forms for decorative pillars with zero defects.
Foundation Formwork: For strip or raft foundations, portable and economical. A Yazd warehouse cut transport costs with our recycled forms, manufactured in Iran.
Special Structures: Custom forms for pools, manholes, stairs, or bridges, like a Mazandaran pool with perfect finishes, crafted locally.
In a Mashhad high-rise, our ABS lever forms, produced in Iran, sped up slab casting by 30%, while in a Karaj villa, prismatic columns saved setup time. Polymer formwork’s versatility, made in Iran, meets every construction need.
Why Polymer Formwork is a Construction Game-Changer
Polymer formwork is a game-changer in construction, offering safety, efficiency, and eco-friendliness. Weak formwork risks leaks or collapses—imagine a column failing mid-pour! Manufactured in Iran by Alborz Formwork, our plastic concrete formwork, with weights as low as 5.2 kg (50×100 cm) or 11 kg (60×120 cm ABS), resists moisture, chemicals, and rust, delivering high-quality finishes without corrosion worries. Its rapid assembly—using red PA66 levers or pins—and reusability (up to 100 cycles with ABS) make the plastic formwork price a smart long-term investment.
In a Tehran tower, our ABS forms, made in Iran, delivered perfect exposed concrete walls, eliminating smoothing costs and showcasing Iranian production quality. In North Iran’s humid climate, they outlasted metal forms without rusting, saving 15% on upkeep—a testament to local craftsmanship.
At Alborz Formwork, we craft polymer formwork for walls, columns, slabs, and more, reducing labor and material costs while boosting sustainability. Ready to explore plastic formwork price or purchase from Iran? Contact us at +98 912 139 0683 for expert support!
Manufacturing Process of Plastic Concrete Formwork in Iran
Producing plastic concrete formwork is a precision-driven process leveraging advanced polymer technology, all manufactured in Iran at Alborz Formwork’s state-of-the-art facilities:
Design Phase: Panels (e.g., 60×120 cm) are engineered for specific uses—walls, columns, slabs—with lever or pin slots for fast assembly. Our Iranian engineers ensure forms meet pressures like 80 kN/m² (ABS), tailored for local and global projects.
Material Selection: ABS (high strength), PP (balanced), PE (affordable), or recycled polymers are chosen—ABS for durability, recycled for cost—all sourced and processed in Iran with quality control.
Injection Molding: Polymers are melted (e.g., 220°C for ABS) and injected into custom molds using Iranian machinery, producing uniform panels with exact dimensions in one step—faster than metal’s multi-stage process.
Quality Testing: Forms undergo pressure tests (up to 80 kN/m² for ABS), flexibility checks, and surface inspections in our Iranian labs to ensure field performance.
Packaging and Delivery: Lightweight forms (e.g., 11 kg ABS) are packaged and shipped from our factories in Tehran, Karaj, Isfahan, and Yazd, ensuring quick access for those purchasing from Iran.
In a Karaj project, our ABS forms, manufactured in Iran, resisted a 6-meter pour without flaws, delivering a finish timber couldn’t match. Plastic’s single-step molding, perfected in Iran, outpaces metal’s complexity.
Types of Polymer Formwork Manufactured in Iran by Alborz Formwork
Manufactured in Iran by Alborz Formwork, our polymer formwork systems are tailored to modern construction needs:
1. Plastic Modular Ledge 5 Formwork (Pin-Type)
Specifications: Sizes like 50×100 cm (5.2 kg) and 15×100 cm (1.8 kg), white (new) or black (recycled), connectable to metal with pins/wedges or levers, produced in our Iranian factories.
Advantages: Ultra-light, versatile, reusable up to 60 times, affordable for hybrid setups—all crafted with Iranian precision.
Applications: Shear walls, dala slabs, foundations. A Tehran apartment cut wall setup time by 25% with these forms, made in Iran.
2. Plastic Modular Lever Ledge 8 Formwork (ABS/PP)
Specifications: 60×120 cm (11 kg ABS, 9.1 kg PP) to 60×20 cm, with red PA66 levers, ABS up to 80 kN/m², PP lighter and softer, manufactured in Iran with advanced tech.
Advantages: Silent, rapid assembly (no hammering), durable, smooth finish for exposed concrete, up to 100 uses with ABS—all benefits of Iranian production.
Applications: High walls, columns, large slabs. A Shiraz tower used our ABS lever forms, made in Iran, for flawless 6-meter walls.
3. Plastic Prismatic Column Formwork
Specifications: Adjustable from 20×20 cm to 60×60 cm, ~80 kg/set, with multiple bolt holes for stability, ABS or PP options, crafted in our Iranian plants.
Advantages: Highly flexible, lightweight, easy stripping, adaptable for square, rectangular, or L-shaped columns—showcasing Iranian innovation.
Applications: Structural or decorative columns. An Isfahan villa showcased intricate pillars with zero defects using these forms, manufactured in Iran.
In a Mashhad factory, our ledge 5 forms, produced in Iran, paired with metal for a hybrid foundation, saving costs. In a Tehran tower, ABS lever forms, made locally, delivered silent, fast wall assembly.
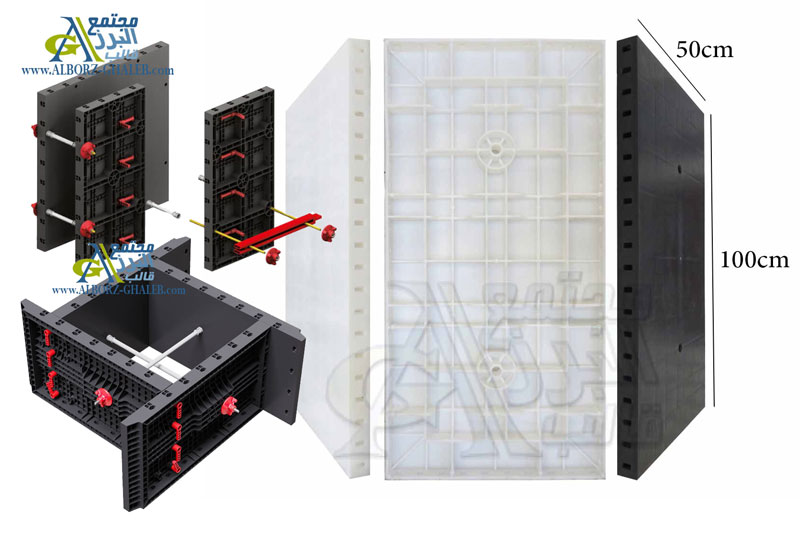
Benefits and Drawbacks of Plastic Concrete Formwork
Drawbacks
Lower Load Capacity: Up to 80 kN/m² (ABS) vs. metal’s higher limits, needs bracing for heavy pours—metal wins in dams.
Non-Repairable: Breaks can’t be fixed, but we replace at 50% cost, easing concerns with our Iranian support.
Heat Sensitivity: Above 80°C may soften, unlike metal—care needed in summer pours.
Benefits
Lightweight Design: 10-16 kg/m² vs. 40 kg/m² metal, easy handling—no cranes needed, as in a Tehran high-rise, all manufactured in Iran.
Non-Stick Finish: Minimal adhesion, fast stripping without oil, saved 20% labor in a Mazandaran pool—a perk of Iranian production.
Rust-Free: Ideal for humid North Iran, unlike metal needing constant care—our Iranian forms shine here.
Affordable: Competitive plastic formwork price vs. metal, perfect for small projects, made in Iran for cost savings.
Quick Setup: Lever or pin systems cut time by 30%, proven in Shiraz slabs, thanks to Iranian design.
Eco-Friendly: Recyclable, with our 50% trade-in for broken forms, reducing waste—a sustainable Iranian solution.
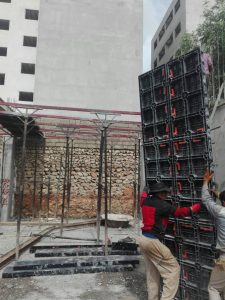
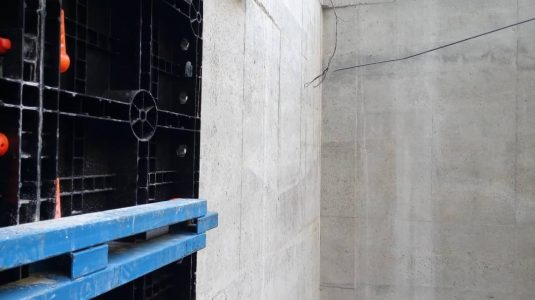
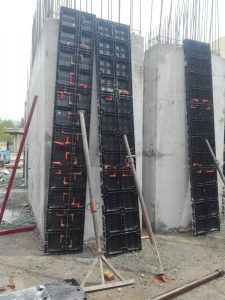
Maintenance Tips for Polymer Formwork
To extend your polymer formwork’s life, manufactured in Iran:
Clean Simply: Use water and mild soap post-use—no harsh chemicals, as in a Tehran project for 80 cycles.
Avoid High Heat: Store below 80°C to prevent warping, unlike metal’s tolerance—our Iranian forms are optimized for this.
Dry Storage: Keep shaded and dry to maintain shape, simpler than metal’s rust-proofing—a benefit of Iranian production.
Handle Gently: Avoid drops to prevent cracks; we replace at 50% cost if damaged—our Iranian commitment.

The advantages of using wall plastic formwork include:
1. Lightweight and easy to handle: The plastic materials used in the formwork are lightweight, making it easy to handle and move around the construction site.
Overall, wall plastic formwork is a popular choice for construction projects due to its ease of use, durability, and cost-effectiveness.
Why Alborz Formwork Excels Globally
Manufactured in Iran, Alborz Formwork delivers durable, affordable polymer formwork with direct shipping from Tehran, Karaj, Isfahan, and Yazd. Our ABS forms rival Geoplast’s strength at a lower cost, and recycled options outprice K-Form. Purchase from Iran for fast, cost-effective solutions—call +98 912 139 0683 today!
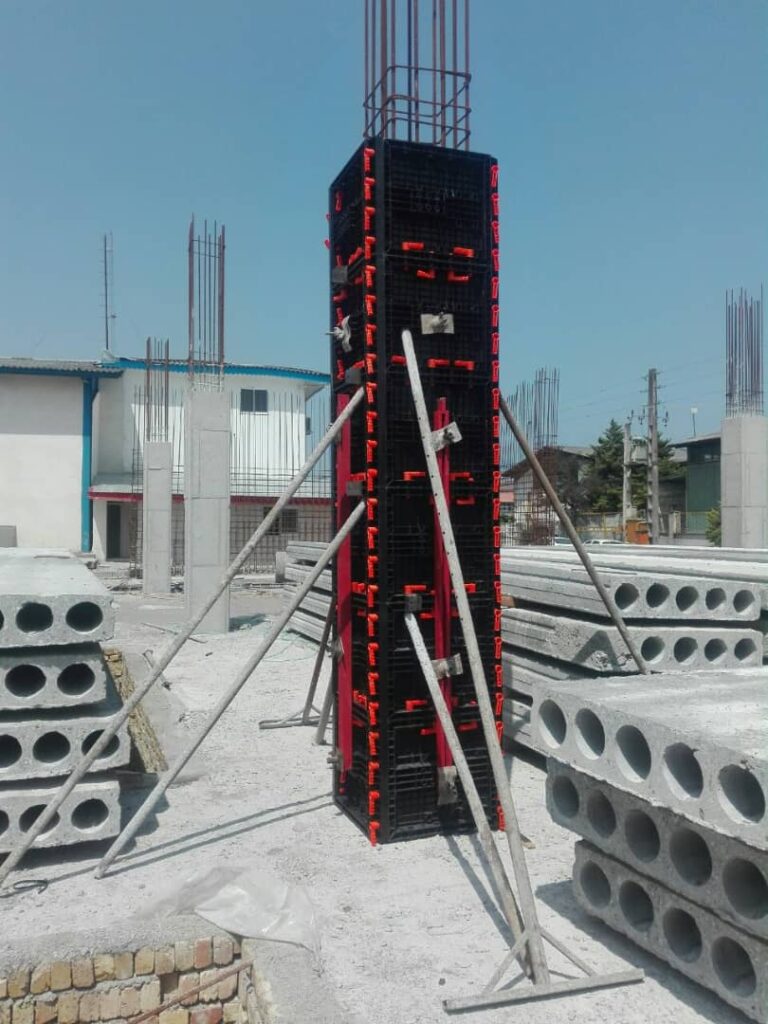
COLUMN PLASTIC FORMWORK
for square and rectangular concrete columns – is an adjustable, lightweight, modular plastic formwork system ideal for unique form configurations.
The Star plastic column formwork system for concrete structures is a universal solution for the forming of columns, pile caps, footings, plinths, and more.
Star panels are connected using the nylon handle with a simple 90 degree twist. Tie rods and anchor nuts are used to prevent bulging on larger width columns.
Form columns from 200 – 1000 mm wide in 105 different size combinations
Because the Star column formwork system is made from high-strength, lightweight ABS at less than 10 kg per piece, crane time can be drastically reduced.
Smart formworkers are experiencing a significant saving of time and resource costs to their jobs.
.ABS
1 | Ap 120 | flat panel | 60 120 | 11 KG |
2 | Ap 20 | flat panel | 60 20 | 2.1 KG |
3 | Ap 25 | flat panel | 60 25 | 2.5 KG |
4 | Ap 30 | flat panel | 60 30 | 3.1 KG |
5 | Ap 35 | flat panel | 60 35 | 3.6 KG |
6 | Ap 40 | flat panel | 60 40 | 4.1 KG |
7 | Ap IN | in | 60 in | 2.1 KG |
8 | Ap OUT | out | 60 out | 2.8 KG |
9 | HDL | — | — | — |
PP
1 | Pp 120 | flat panel | 60* 120 | 9.1 KG |
2 | Pp 20 | flat panel | 60* 20 | 1.8 KG |
3 | Pp 25 | flat panel | 60* 25 | 2.2 KG |
4 | Pp 30 | flat panel | 60* 30 | 2.5 KG |
5 | Pp 35 | flat panel | 60* 35 | 3.0 KG |
6 | Pp 40 | flat panel | 60* 40 | 4.1 KG |
7 | Pp IN | in | 60* in | 2.0 KG |
8 | Pp OUT | out | 60* out | 2.6 KG |
9 | HDL | — | — | — |
Advantages and Disadvantages Plastic formwork products
Advantages Plastic formwork products
Easy to demould. The concrete does not stick to the board surface, no release agent is required, and it is easy to demould and clean the dust.
It is light in weight and has strong process adaptability. It can be sawed, planed, drilled, nailed, and can be formed into any geometric shape at will to meet the needs of building formwork of various shapes.
The formwork is spliced tightly and flatly, and the surface degree and smoothness of the concrete structure after demoulding exceed the technical requirements of the existing clear water formwork, and there is no need for secondary plastering, saving labor and materials.
Disadvantages Plastic formwork products
The static bending strength and static bending elastic modulus of plastic building formwork are smaller than other formwork.
At present, the plastic building formwork is mainly used as the roof and floor formwork in the form of flat plate, and the bearing capacity is low. As long as the spacing of the secondary beams is properly controlled, the construction requirements can be met. But to be used as wall column formwork, it must be processed into steel frame plastic formwork.
The coefficient of thermal expansion and contraction of plastic sheets is larger than that of aluminum formwork, so plastic building formwork is greatly affected by temperature. For example, in the high temperature period in summer, the temperature difference between day and night can reach 40 °C. Up to 3mm ~ 4mm. To solve the problem of expansion, you can choose an average temperature time to lay the slabs during construction, or add sponge strips between the slabs, which can eliminate the gaps in the formwork, ensure that the pouring concrete does not leak, and can solve the problem of high temperature. Arching problem.
whatsapp: https://wa.me/c/989121390683
web : www.alborz-ghaleb.com
telegram : http://t.me/alborz_ghaleb