Formwork is the beating heart of concrete construction.
Building concrete structures is a complex, multi-step process. One of the most crucial stages, without which all other efforts would be in vain, is formwork. Formwork is essential for shaping and reinforcing concrete, giving it the required strength and stability.
Why Are Concrete Structures So Strong and Durable?
The answer lies in a vital stage called formwork, carried out using concrete molds. Formwork gives shape to fresh concrete and reinforces it so it can bear its own weight and support other structural elements.
Definition and Purpose of Formwork
Formwork is the process of using temporary molds, called forms, to shape freshly poured concrete. These molds, like baking molds, give concrete its desired shape and dimensions. For instance, a cylindrical form is used to create a sturdy, round column, while angled forms are used for sloped roofs. The primary purpose of formwork is to hold the fresh concrete in place until it hardens and achieves the exact shape and dimensions needed.
Not only does formwork shape the concrete, but it also plays a critical role in ensuring the building’s quality and durability. Poorly executed formwork can lead to cracks, deformities, and structural weaknesses.
Formwork comes in various types, each with specific features and suitable applications. The choice of form depends on factors like project size, design complexity, budget, and timeline.
- Timber Formwork:
- The oldest and most commonly used type.
- Made from materials like plywood.
- Offers high flexibility, making it ideal for complex designs.
- However, it is not resistant to moisture and may warp over time.
- Metal Formwork:
- Usually made of steel.
- Suitable for large-scale industrial projects.
- Extremely durable and reusable.
- Heavyweight, requiring special equipment for handling.
- Plastic Formwork:
- Made from materials like polyethylene.
- Lightweight and ideal for smooth and precise surfaces.
- Commonly used in precast projects.
- Self-Releasing Formwork:
- A modern innovation that detaches automatically from the concrete.
- Speeds up construction and reduces labor costs.
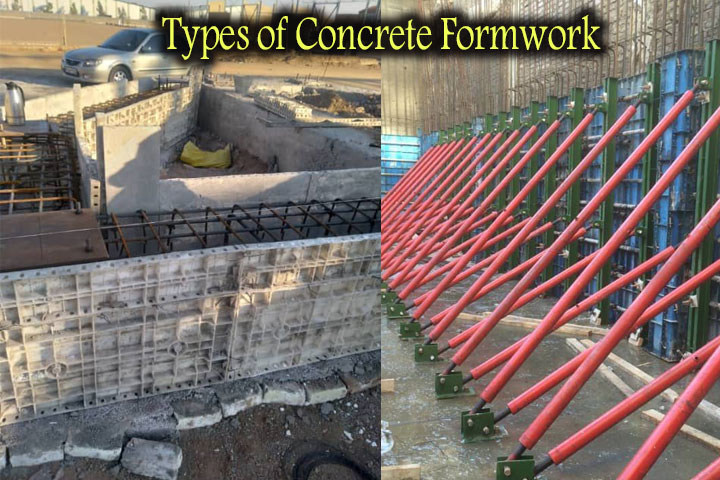
Steps to Build a Concrete Structure Using Formwork
Form Design:
Engineers design the forms based on building blueprints, similar to crafting a mold for a cake.Form Construction:
Forms are built using materials like wood, metal, or plastic. This step corresponds to creating a cake mold from cardboard or metal.Form Installation:
The forms are precisely installed at the site using various tools. This is akin to placing a cake mold in the baking tray. Connections and supports are used to secure the forms in place.Pouring Concrete:
Concrete is carefully poured into the forms, ensuring an even spread without air bubbles.Concrete Vibration:
Vibrators are used to eliminate air bubbles, making the concrete denser and stronger.Curing Concrete:
Concrete remains in the forms for a specified period to harden completely. This duration depends on factors like concrete type, weather conditions, and structural dimensions.Removing Forms:
Once hardened, the forms are gently removed to avoid damaging the concrete.Building a concrete structure is much like baking a cake, where the mold shapes the final product. The general process includes:
Key Considerations in Formwork Execution
Accuracy in Dimensions:
Forms must match the exact dimensions of the design to ensure the desired shape and size.Securing Forms:
Forms should be tightly connected and anchored to prevent displacement during concrete pouring.Monitoring Concrete Quality:
Regular checks on concrete quality ensure its strength and durability.Safety Measures:
Workers must use proper safety equipment and follow safety guidelines.
By adhering to these steps and precautions, high-quality and durable concrete structures can be built.
Benefits of Using Formwork
Formwork not only shapes concrete but also offers several other advantages:
- Increased Speed and Quality: Accurate and standard formwork speeds up construction while improving the structure’s quality.
- Cost Reduction: Reduces concrete waste, minimizes labor costs, and extends the building’s lifespan, ultimately lowering overall project expenses.
- Uniform Structures: Ensures that all concrete components have consistent shape and size.
- Complex Designs: Enables the execution of intricate and diverse architectural designs using modern prefabricated forms.
Challenges and Solutions
While formwork has numerous benefits, it also comes with challenges:
- High Initial Costs: Purchasing or renting forms can be expensive.
- Installation Issues: Setting up forms requires precision and expertise.
- Wear and Tear: Frequent use can damage forms over time.
Solutions:
- Rent Instead of Buy: Renting forms can be more economical for smaller projects.
- Use Lighter Forms: Plastic and composite forms are easier to install.
- Simplify Designs: Simpler form designs facilitate easier installation and removal.
- Proper Maintenance: Clean and maintain forms after every use.
- High-Quality Materials: Using superior materials extends the life of forms.
Safety in Formwork
Safety is paramount during formwork execution. Workers should use appropriate safety gear and follow these guidelines:
- Secure Scaffolding: Use reliable scaffolding for work at height.
- Safety Equipment: Wear helmets, gloves, and safety boots to protect against head, hand, and foot injuries.
- Life Jackets: Use near water or high elevations.
- Equipment Checks: Ensure safety equipment is in good working condition before use.
Conclusion
Formwork is one of the most critical stages in building concrete structures, significantly impacting the project’s quality, speed, and cost. By following safety protocols and proper methods, the benefits of formwork can be maximized.
FAQs
Forms can be made of wood, metal, plastic, or modern self-releasing materials, each suited for different projects.
High costs, installation precision, and form durability are common challenges.
Consider factors like project size, design complexity, budget, and timeline.
Yes, larger projects often require durable, reusable, and more advanced formwork systems.