Plastic injection molding is a revolutionary technology for producing high-precision polymeric concrete formwork, offering durability, lightweight design, and cost-efficiency for construction projects. This guide provides an in-depth look at the history, production process, materials, advantages, design principles, and costs associated with creating plastic concrete formwork systems. Designed for engineers, contractors, and construction enthusiasts, this article aims to illuminate the benefits and technical aspects of this advanced manufacturing method.
What is Plastic Injection Molding?
Plastic injection molding involves injecting molten plastic into a precisely designed mold, where it cools and solidifies into the desired shape. This process is widely used to produce polymeric concrete formwork, which serves as a lightweight, reusable alternative to traditional wooden or metal formwork. Plastic formwork systems are prized for their resistance to moisture, ease of handling, and ability to maintain structural integrity in demanding construction environments.
History of Plastic Injection Molding
The origins of plastic injection molding date back to 1867, when John Wesley Hyatt used it to create celluloid billiard balls by injecting the material into a mold. In 1872, the first rudimentary injection molding machine was developed, laying the groundwork for modern manufacturing. While early machines were basic, today’s sophisticated equipment can produce everything from intricate components to robust plastic concrete formwork systems, transforming the construction industry.
Advantages of Plastic Injection Molding for Concrete Formwork
Plastic injection molding offers significant benefits for producing polymeric concrete formwork, making it a preferred choice in modern construction.
High Production Speed
Injection molding machines can produce large quantities of formwork in minimal time, ideal for large-scale projects requiring multiple units. This efficiency reduces project timelines and labor costs.
Precision and Quality
The process ensures high dimensional accuracy, critical for concrete formwork where even minor deviations can compromise structural integrity. Precision molding results in consistent, high-quality formwork.
Design Versatility
Injection molding allows for complex and customized formwork designs, enabling architects and engineers to implement innovative structural solutions in concrete construction.
Durability and Resistance
Polymeric formwork produced via injection molding is resistant to moisture, chemicals, and mechanical stress, ensuring long-term durability and reduced maintenance costs. Learn more about these benefits at plastic concrete formwork systems.
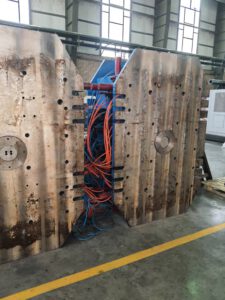
Production Process of Polymeric Concrete Formwork
The production of polymeric concrete formwork through plastic injection molding involves four key stages, each requiring precision and expertise.
1. Mold and Machine Preparation
The process begins with preparing the injection molding machine and mold. Molds, typically made from alloy steel or aluminum, consist of fixed and movable parts that must be perfectly aligned. Any misalignment can lead to defective formwork. Molds are often crafted using advanced CNC machines for maximum accuracy.
2. Material Feeding and Injection
Thermoplastic materials are fed into the machine, where they are heated to a molten state and injected into the mold under high pressure. This stage demands precise control of temperature and pressure to ensure uniform material distribution and accurate formwork shaping.
3. Cooling
After injection, the molten plastic is cooled gradually to solidify into the mold’s shape. Controlled cooling is essential to prevent warping or dimensional inaccuracies. Dimensional tolerances are carefully monitored to ensure the formwork meets design specifications.
4. Ejection and Final Inspection
Once cooled, the formwork is ejected from the mold. It must be fully solidified to avoid deformation during ejection. The finished formwork undergoes rigorous inspection to verify quality and precision, ensuring it meets construction standards.
Materials Used in Injection Molding for Concrete Formwork
The versatility of injection molding lies in its ability to use a wide range of thermoplastic materials, each suited to specific formwork requirements.
Common Thermoplastics
- ABS: Known for high strength and affordability, ideal for durable formwork but less resistant to solvents.
- Nylon: Offers excellent chemical and moisture resistance, suitable for industrial formwork applications.
- HDPE: Used for lightweight, impact-resistant formwork, though with lower overall strength.
- Delrin: High stiffness and self-lubricating properties make it ideal for complex molds, but it may warp during molding.
- Polycarbonate: Resistant to heat and impact but prone to cracking under stress.
- ABS/PC Blend: Combines ABS and polycarbonate for enhanced heat and impact resistance.
- PEI: Highly resistant to fire and heat, though expensive, offering exceptional longevity.
- PEEK: Superior mechanical and chemical resistance, ideal for high-performance formwork but costly.
- Polystyrene: Low-cost but low-quality, suitable for non-critical applications.
- Polypropylene: Chemically resistant but prone to production errors.
Selecting the right material for plastic concrete formwork systems depends on project requirements, environmental conditions, and budget constraints.
Polishing and Finishing Techniques
Post-production polishing and finishing enhance the surface quality of polymeric formwork, removing minor imperfections. Common techniques are summarized below:
Technique | Application | Characteristics |
---|---|---|
Basic Polishing | Thick, non-precision formwork | May leave machining marks. |
Sanded Polishing | Removes machining lines | Sanding marks may remain visible. |
Diamond Polishing | Smooth, glossy surfaces | Eliminates sanding marks. |
Sandblasting | Mirror-like finishes | Flawless, high-quality surface. |
Design Principles for Injection Molding Molds
Effective mold design is critical to producing high-quality polymeric formwork. Key principles include:
Machine Type
Injection molding machines are either horizontal or vertical, influencing mold design and configuration.
Injection Location
The entry point and direction of material injection must be optimized to prevent defects in the formwork.
Material Transfer Method
Material can be transferred via screw or piston systems, each requiring specific mold design considerations.
Movable Plate Movement
The mold must accommodate the machine’s movable plate, which may operate via jack or arm mechanisms.
Cost Analysis of Polymeric Formwork Production
The cost of producing polymeric concrete formwork depends on several factors:
- Raw Materials: The type and volume of thermoplastics (e.g., ABS, PEEK) significantly impact costs.
- Mold Fabrication: CNC-machined steel or aluminum molds are expensive, with production times ranging from one to several months.
- Labor and Equipment: Skilled operators and advanced machinery add to production costs.
Cost Formula: Total Cost = Raw Material Cost + Mold Fabrication Cost + Labor and Equipment Cost
Using cost-effective materials and optimized designs, such as those offered by plastic concrete formwork systems, can help manage expenses.
Investment Requirements for Starting an Injection Molding Business
Launching a plastic injection molding operation requires substantial investment:
- Injection Molding Machine: Starting at $15,000 for basic models.
- Facility Costs: Approximately $6,000 for leasing and utilities.
- Mold Costs: At least $1,000 per mold, depending on complexity.
- Raw Materials: Starting at $0.50 per kilogram for affordable options like polyethylene.
The minimum investment is around $25,000, though costs can escalate with higher-quality equipment and larger-scale operations.
Revenue Potential of Injection Molding
The injection molding industry, particularly for polymeric formwork, offers significant revenue potential due to growing demand in construction. With advanced equipment and skilled labor, daily profits can exceed $300. However, success requires expertise, making it unsuitable for inexperienced entrepreneurs.
Is Home-Based Injection Molding Feasible?
While technically possible, home-based injection molding requires specialized equipment, adequate space, and technical knowledge. Resources like “Secrets of Building an Injection Molding Machine” can provide further guidance.
Conclusion
Plastic injection molding is a game-changer for producing polymeric concrete formwork, offering unmatched precision, durability, and efficiency. By selecting appropriate materials, adhering to sound design principles, and leveraging advanced equipment, construction professionals can achieve superior results. For high-quality formwork solutions, explore plastic concrete formwork systems.
Frequently Asked Questions
What is plastic injection molding?
It’s a manufacturing process where molten plastic is injected into a mold to create precise components, such as concrete formwork.
Why use plastic formwork for concrete?
Plastic formwork is lightweight, moisture-resistant, and reusable, reducing costs and improving efficiency.
Which materials are best for injection molding?
ABS, nylon, HDPE, and polycarbonate are popular due to their strength and versatility.